DC Continuous Distillation Pilot Plant vocational training equipment
The solution having to be distilled, stored in a glass tank, is sent to the distillation column by a metering pump after crossing a pre-heating exchanger. The column can be fed through 3 points at different height.
Training program
This unit enables to deepen the following issues:
• Distillation of different mixtures (water / ethanol, water / methanol, methanol / propanol, etc…) versus the variation of the following operational parameters:
• feed pre-heating temperature
• reflux ratio
• feeding flow rate
• reboiler heating power
• feeding composition
• residual pressure
• Mass balance
• Energy balance
• Flooding
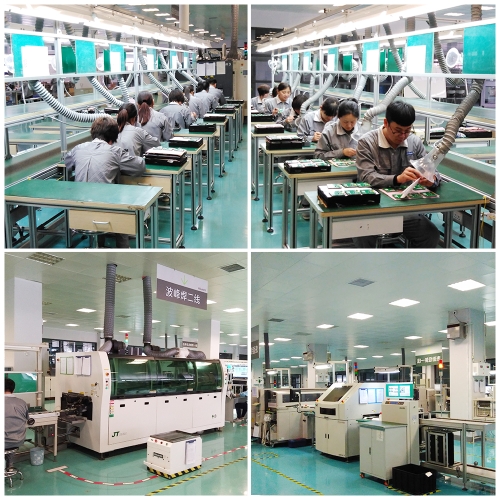
• Calculation of the number of theoretical trays
TECHNICAL SPECIFICATIONS:
Mod. DC
• Framework of AISI 304 stainless steel with castors
• 15 l feeding tank of borosilicate glass
• Distillation column of borosilicate glass, DN 50, h = 1100 mm, packed with mesh of AISI 316 stainless steel
• Reflux head of borosilicate glass equipped with solenoid valve for the control of reflux ratio
• Reboiler of borosilicate glass, with capacity of 5 l, equipped with quartz-sheathed electric heater of 2.5 kW
• Over head condenser of borosilicate glass, with exchange surface of 0.4 m2
• 2 graduated vessels of borosilicate glass for collecting the bottom product (4 l) and the distillate (1 l)
• Tube-in-tube heat exchanger of stainless steel for the bottom product
• Liquid-ring vacuum pump, equipped with air/water separator and check valve
• Feeding metering pump of AISI 316 stainless steel, with max. flow rate of 12 l/h
• Flowmeter of AISI 304 stainless steel for measuring the flow rate to the condenser, range of 0 to 250 l/h (for mod. DC, only)
• 2 Thyristor units
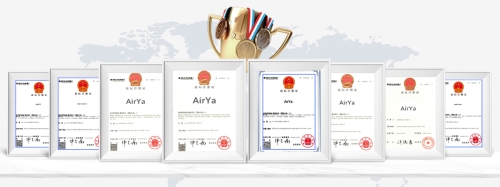
• Vacuum gauge of AISI 304 stainless steel with range of
-1 to 0 bar
• 2 programmable timers for the control of reflux ratio
• 12 thermoresistances Pt 100, with sheath of AISI 316 stainless steel
• 12 electronic temperature indicators
• Electronic differential pressure transmitter (between column top and bottom) of AISI 316 stainless steel, with range of 0 to 200 mm H2O, 4-20 mA output signal
• Electronic indicator of the measure of differential pressure
• Quartz-sheathed electric heater for preheating the feeding mixture, P = 0.3 kW
• Piping and valves of AISI 304 and AISI 316 stainless steel
• Switchboard IP55, complying with EC conformity mark, including plant synoptic and ELCB
• Emergency button
Supply with
THEORETICAL – EXPERIMENTAL HANDBOOK