AFO041 Oil Filtration System,Oil Purification System For The Steel Plants
Impurities: <1μm
Work pressure: 0.6~1Mpa
Payment Terms: TT , LC , Others
Oil filtration systems are essential in steel plants to ensure smooth machinery operation and to prevent machinery failures caused by contaminated oil. Steel plants rely on heavy machinery for the production process, and these machines require lubrication to function correctly. However, lubrication oil can become contaminated with dirt, dust, metal shavings, and water, which can impair its effectiveness and lead to machinery failures. In this article, we will explore the role of oil filtration systems in steel plants and their benefits.
The Steel Industry
The steel industry is a highly competitive sector that produces materials for construction, manufacturing, and infrastructure projects. The production process is complex and involves the use of large, heavy machinery. Steel plants must maintain efficient and reliable machinery operation to meet production targets and avoid costly downtime.
The Role of Lubricating Oil
Lubricating oil is vital to the efficient and reliable operation of machinery in steel plants. It reduces friction between moving parts, preventing wear and tear and protecting machinery from damage. Lubricating oil also reduces heat buildup, preventing machinery from overheating and failing prematurely.
Contaminants in Lubricating Oil
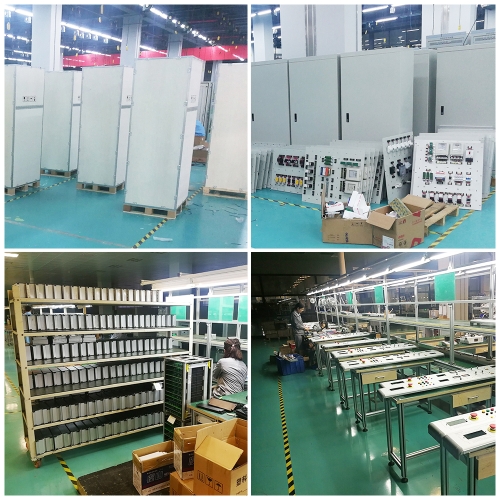
Contaminants in lubricating oil can impair its effectiveness, leading to machinery failures and downtime. Contaminants can come from many sources, such as dirt and dust, metal shavings, and water. These contaminants can cause machinery to wear out prematurely, reduce efficiency, and increase maintenance costs.
Oil Filtration Systems
Oil filtration systems are designed to remove contaminants from lubricating oil, improving its quality and extending its lifespan. There are several types of oil filtration systems used in steel plants, including gravity filtration, centrifugal filtration, magnetic filtration, and vacuum dehydration systems.
Gravity filtration systems use gravity to filter oil through a series of filters that remove contaminants as the oil flows down through the system. Centrifugal filtration systems use centrifugal force to separate contaminants from oil. The oil is forced through a series of filters at high speed, which separates contaminants from the oil. Magnetic filtration systems use magnets to remove metallic particles from the oil. The oil flows through a series of magnets that attract and remove metal shavings and other metallic particles. Vacuum dehydration systems remove water from the oil by creating a vacuum in the filtration chamber. The water is evaporated from the oil, leaving it free of water and other contaminants.
Oil filtration systems offer many benefits to steel plants, including:
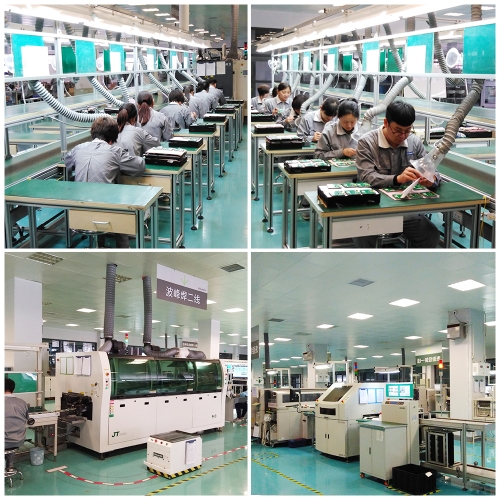
Improved quality of lubricating oil: Oil filtration systems remove contaminants from lubricating oil, improving its quality. High-quality lubricating oil reduces friction between moving parts, preventing wear and tear and protecting machinery from damage.
Extended machinery lifespan: By removing contaminants from lubricating oil, machinery operates more efficiently and lasts longer. This reduces maintenance costs and increases equipment lifespan.
Reduced maintenance costs: By removing contaminants from lubricating oil, machinery requires less maintenance and repair work. This reduces maintenance costs and increases equipment lifespan.
Improved machinery performance: By removing contaminants from lubricating oil, machinery runs more efficiently, reducing energy consumption and increasing productivity. Improved machinery performance also results in fewer breakdowns and less downtime.
In conclusion, oil filtration systems play a crucial role in ensuring the efficient and reliable operation of machinery in steel plants. Contaminants in lubricating oil can cause machinery to wear out prematurely, reduce efficiency, and increase maintenance costs. Oil filtration systems remove contaminants from lubricating oil, improving its quality, and extending the lifespan of machinery. This reduces maintenance costs, increases equipment lifespan, and improves machinery performance, resulting in a more productive and efficient steel plant.